G-Button Securement Children's Hospital Colorado
August 2016 - Present
A G-Button is a low-profile plastic tube that is surgically inserted into the patient through a small incision in the abdominal wall and stomach. The G-Button allows food, supplements, and medicine to pass directly into the stomach. Even though the placement of a G-Button is a fairly simple procedure, there are postoperative complications that arise from this treatment. Most commonly, there is the formation of granulation tissue and leakage of stomach contents around the device. These issues arise from a lack of securement between the device and the patient.
This project addresses the lack of efficient securement options for G-Buttons by focusing on creating an attachment that will prevent any significant movement of the button, while maintaining comfort for the user.
Thus far, my classmates and I have designed the aesthetics, functionality, and usability of the device. In addition to the overall design, my responsibilities include the initiation, planning, execution, monitoring, controlling, and closure of the project.
This device is still under development. Proprietary information restrictions inhibit any further details and images of the device.
Après Tune - Portable Quick Tuner
January 2016 - May 2016
In order to sustain maximum performance over a prolonged period of time, all sports equipment must be maintained in some way or another. Skis are no different. In fact, it is recommended that skis undergo some sort of tune-up every third trip to the mountain. This tune-up, however, is not viewed as a convenient process. It can take up to an hour and a half for a basic tune. A manual tune-up can become costly and time consuming. As such, two of my peers and I saw a need to create a process that makes tuning more efficient and user friendly in order to inspire more skiers to perform the task themselves.
The product we created is a portable tuning device capable of easily and symmetrically filing down the edges of a ski to a specified side-edge bevel angle between 0-3°, while remaining untethered by power cords. It has several base attachments that allow the device to be securely attached to a variety of flat surfaces, making it easy to find a spot to use the device. Further development of this device would incorporate a dry waxing feature.
Robotics Project
January 2016 - May 2016
The Advanced Mechatronics & Robotics course at CU Boulder is comprised of a series of labs and a class project. When I took this course, the class-chosen competition was based on the children’s game ‘Hungry Hungry Hippos’. For this project, teams of four had to design and build an autonomous robot that could pick up ping pong balls and project them through a target. In addition to this objective, the robots also had to be able to: detect where the center of the course was, detect where the targets were, determine which of the targets was active, and fit within size restrictions.
My team designed a robot which utilized four Mecanum wheels and DC motors for the drive system, a laser cut acrylic structure, spinners to collect the ping pong balls, a belt system with 3D printed claws to transfer ping pong balls to the second level, and PVC pipes with two counter-spinning foam wheels to project the ping pong balls.
For the project, I designed the ping pong ball acquisition and transfer system, and assisted with the overall design and improvements to the other subsystems.
Mechanics of the Mouse Uterine Cervix
June 2016 - January 2017
Current methods of examining the gestational cervix include digital examination and transvaginal ultrasound cervical length (CL) measurement. While these methods are important in determining risk of preterm birth (PTB), a more quantitative method of measuring cervical mechanical properties could be advantageous in giving clinicians a fuller representation of the cervix during late stage pregnancy. The Ferguson group is currently developing a technique for characterizing pressure and contractility of a rodent cervix, which may lead to translational research and new clinical methods for determining mechanical properties within a human cervix.
My responsibility was to further the development of a balloon catheter that can be inserted into a rodent cervix and inflated radially, via water or another incompressible fluid, and measure the pressure within the balloon using an array of inline external pressure sensors.
This system is still under development. Proprietary information restrictions inhibit any further details and images of the device.
Flexible Thermal Ground Planes
August 2014 - May 2015
Flexible thermal ground planes (TGPs) are passive thermal management devices that utilize fluid convection to achieve high effective conductivity and low thermal resistance. Heat is absorbed into the TGP at an evaporator region, which causes the liquid to evaporate. The heated vapor is carried via convection through the vapor layer to a condenser region where the vapor condenses and heat is expelled. The condensed liquid is then pulled back to the evaporator via capillary forces in the wick, where the cycle can repeat.
In order for flexible TGPs to function efficiently they require a permanent flexible structure that enables a 90° bend without cracking. This flexible structure was the focal point of my research. Using a combination of polymers and photoresists to create the structure and testing the flexibility post atomic layer deposition (ALD), I sought to determine the best method to achieve a flexible TGP. However, my findings indicated that the hypothesized method was unreliable, and as a result, the project shifted upon the completion of my research.
This system is still under development. Proprietary information restrictions inhibit any further details and images of the device.
Drill Powered Tricycle
August 2014 - December 2014
The purpose of this project was to utilize various analysis techniques to create a drill powered tricycle that was both aesthetically pleasing and functional under various design constraints. To begin with, the drill powered vehicle could not exceed 3’6” tall including the height of the driver. It also had to complete a predetermined course of length 1,370 feet and elevation change of 45 feet, and had to include at least two wheels with a minimum wheelbase of 30 inches.
In order to create an effective design based off of these requirements, my team sought to create a simple design that used a pre-fabricated frame with as few modifications as necessary. And since I had more advanced knowledge of bicycle part mechanics, I designed both the drive train and the rear axle assembly. Furthermore, I was responsible for all of the welding and tasks inherent to the overall fabrication of the vehicle.
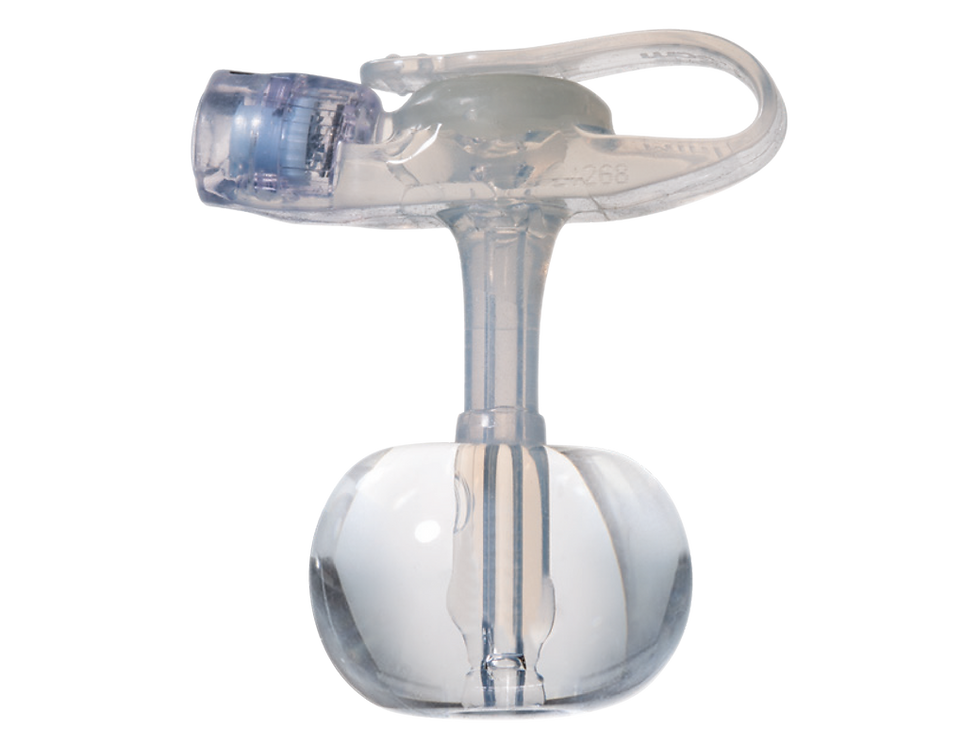


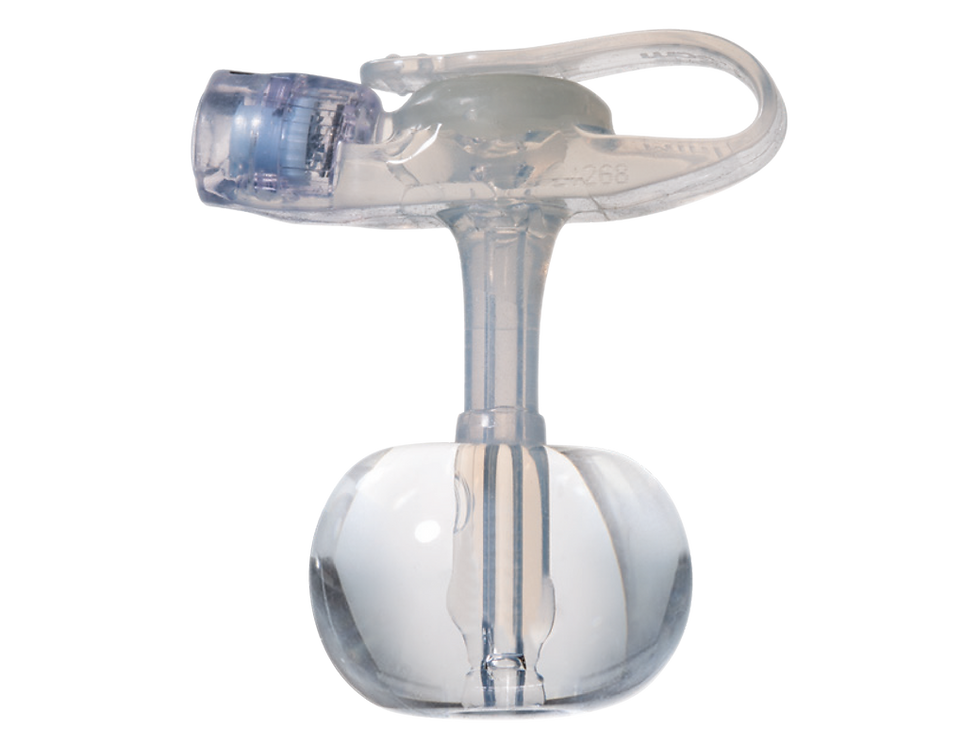

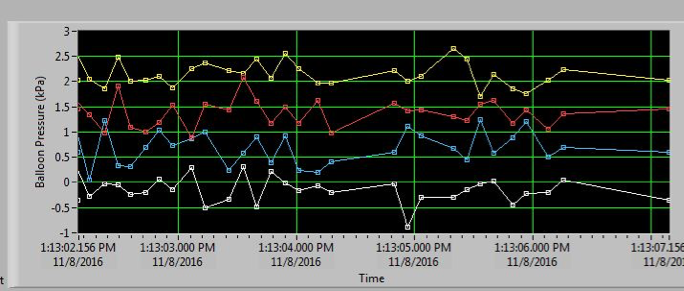


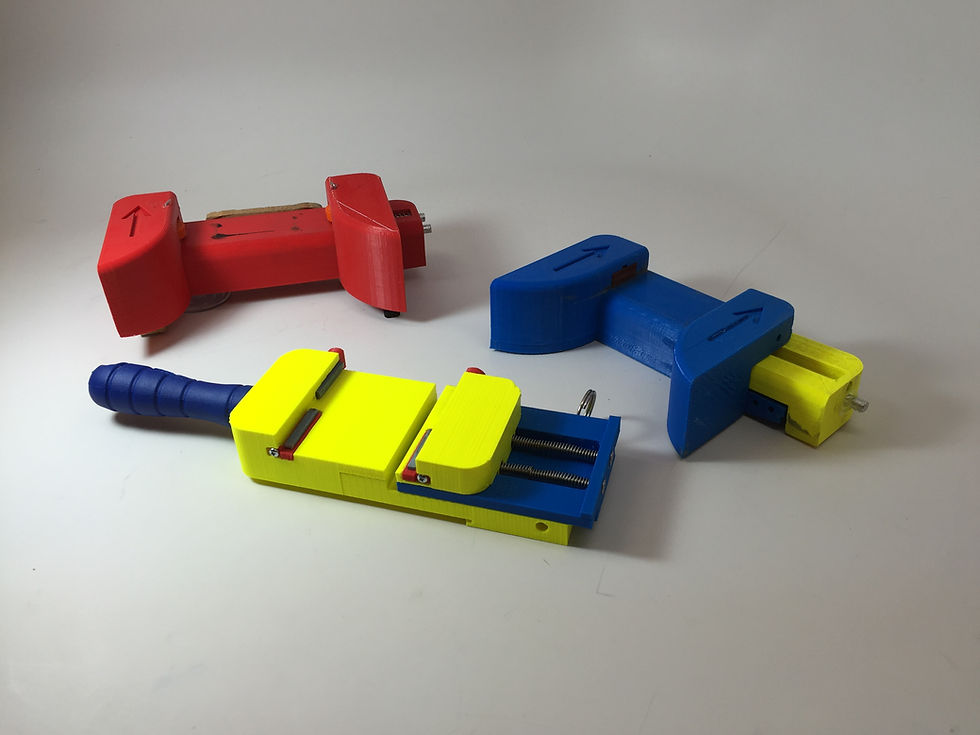


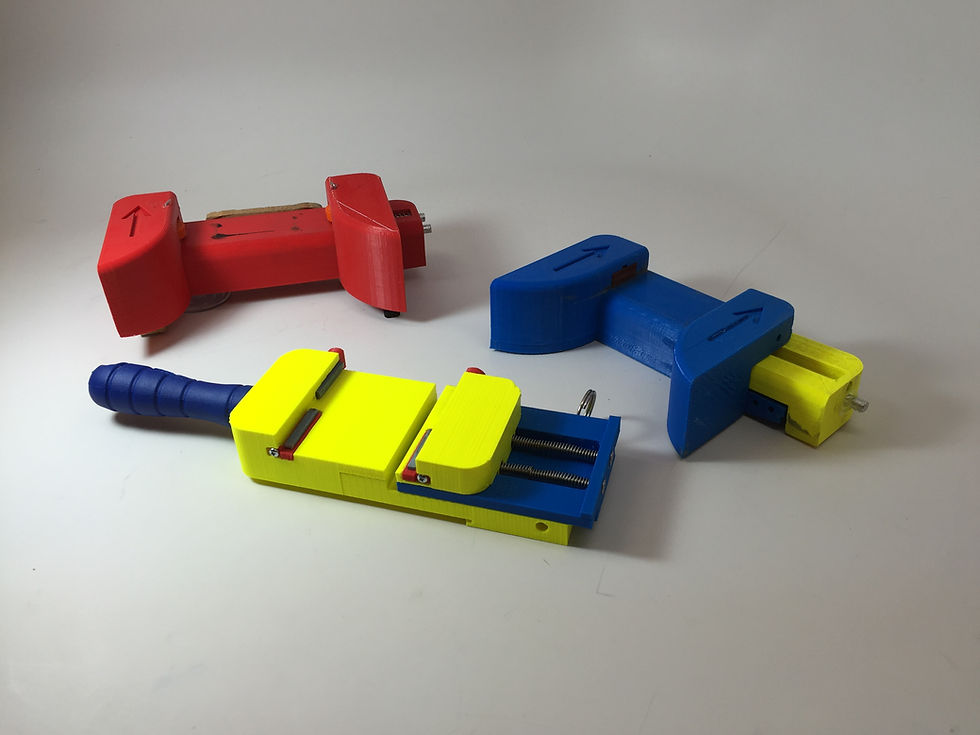





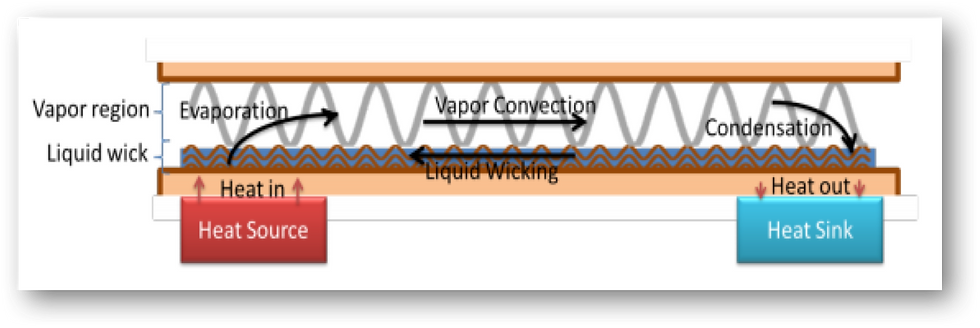



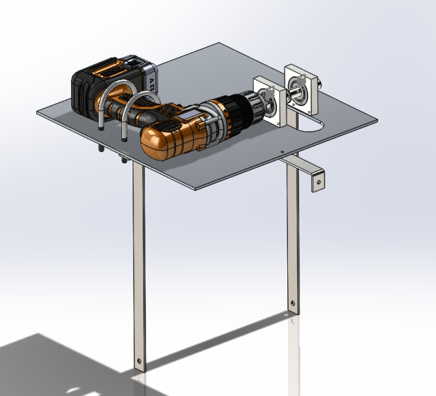
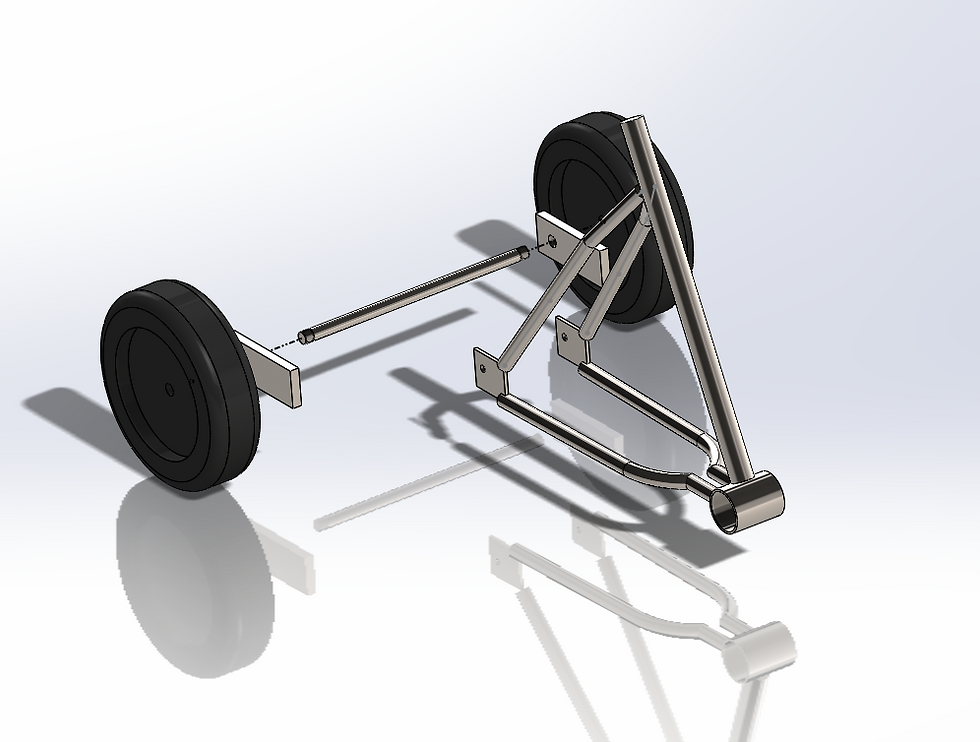
